How do Dry Cast Segmental Retaining Walls (SRW) Compare to Redi-Rock?
When choosing an earth retention solution, wall design and installation professionals can select from several systems. Dry cast segmental retaining walls (SRW), featuring interlocking retaining wall blocks, can be a popular option for select applications based on their relatively basic design and installation requirements.
So how does a dry cast SRW compare to Redi-Rock precast concrete retaining wall? We’ve compared the alternatives across multiple categories to help you decide which solution is the best choice for your project.
The Base Course
Short on time? Here are this article’s key takeaways…
Dry cast segmental retaining walls (SRWs) are often considered for projects alongside Redi-Rock wet cast large block retaining walls.
Dry cast SRW blocks provide a lower product cost, faster manufacturing times, and more readily available inventory.
Redi-Rock wet cast large retaining wall blocks offer the capability to build taller gravity walls, more efficient installation, greater project versatility, and a more natural quarried stone appearance.
Both solutions offer unique advantages with the decision ultimately coming down to the project type and what you consider the products’ most important features.
DESIGN
How easy is it to design with the solution?
Redi-Rock
Multiple Redi-Rock block sizes, types, and styles and robust design resources allow for significant project customization.
Dry Cast SRW
Smaller SRW blocks permit flexibility in design, but can prove challenging for larger-scale projects.
PRODUTION
How are the solutions manufactured?
Redi-Rock
Produced in factory-controlled conditions by pouring wet cast concrete into polyurethane molds affixed to premium-grade steel forms. Redi-Rock blocks cure over hours.
Dry Cast SRW
Manufactured in factory-controlled conditions with high-pressure compression forming blocks out of a dense concrete mix. Dry-cast SRW blocks don’t require significant curing time and are ready to be set shortly after production.
INSTALLATION
What are the solutions’ installation demands?
Redi-Rock
Installed by small crews with excavators. Redi-Rock’s large concrete retaining wall blocks offer installation efficiency and speed.
Dry Cast SRW
Installed by hand or with skid steers or mini excavators. Smaller SRW blocks result in labor-intensive and less efficient installations
VERSATILITY
How adaptable are the solutions?
Redi-Rock
Redi-Rock blocks can be utilized in nearly all site scenarios. Wet cast’s lower porosity makes it an especially good choice for sites with high water tables, poor drainage, or where the wall may be subject to prolonged water exposure.
Dry Cast SRW
SRW blocks can be utilized in most site scenarios. Wet sites that experience freeze-thaw cycles can prove challenging since dry cast’s higher porosity allows water to enter the blocks and expand when frozen, damaging the blocks and shortening their lifespan.
SITE DEMANDS
What site characteristics are required for the solutions?
Redi-Rock
Redi-Rock precast blocks are delivered to the site on-demand – avoiding storage or assembly requirements – and can be installed within small footprints.
Dry Cast SRW
Like Redi-Rock, dry cast SRW blocks can be delivered to the site on-demand – avoiding storage or assembly requirements. Smaller blocks require more time to unload. Dry cast SRWs can be installed within small footprints.
LIVE LOADS
Can the solutions handle live (surcharge) loads like those created by roadways, parking lots, and other infrastructure?
Redi-Rock
Design and construction can be tailored to meet specific live load requirements. Redi-Rock’s Positive Connection (PC) blocks allow for the installation of mechanically stabilized earth (MSE), or reinforced, walls.
Dry Cast SRW
Design and construction can be tailored to meet specific live load requirements. SRWs can accommodate select live loads by using geogrids or soil reinforcement materials.
APPEARANCE
Do the solutions look good?
Redi-Rock
Various deep natural-looking texture options are available thanks to the fluidity of wet cast concrete, which allows the mix to flow more easily into forms and molds during production. Redi-Rock’s deep, rich colors vary by region and manufacturer and are developed especially to emulate the hues of natural, cut-from-the-quarry stone.
Dry Cast SRW
Dry cast’s denser mix and high compression production process limit the depth and detail of the block texture. Common colors for dry cast SRW blocks include shades of gray, beige, brown, and charcoal. Some manufacturers may offer more specialized colors like reds, blues, or greens.
COST
Are the solutions cost-effective?
Redi-Rock
Redi-Rock may be more expensive on the front end than dry cast SRWs, but it offers several benefits dry cast doesn’t. Installation savings, a more natural appearance, and extended life often make Redi-Rock a more compelling choice for those with a long-term view.
Dry Cast SRW
Blocks can be less expensive due to rapid production. Less efficient installation can increase labor costs. Additional excavation and reinforcement requirements for taller SRWs can also increase materials costs and installation.
The Conclusion
It can be challenging to objectively compare wall solutions constructed with Redi-Rock wet cast large retaining wall blocks to walls built with dry cast SRW blocks. Both solutions offer unique advantages. Dry cast SRW blocks provide a lower base product cost, faster manufacturing times, and more readily available inventory. Redi-Rock wet cast large retaining wall blocks offer the capability to build taller gravity walls, more efficient installation, greater project versatility, and a more natural quarried stone appearance. Ultimately, the decision boils down to the project type and what you consider the most important factors.
Dry cast SRWs are great fits for smaller-scale projects where the upfront product cost matters most. Redi-Rock walls make the most sense for larger projects where installation efficiency and finished appearance are priorities. Redi-Rock also suits the project owner who can see the long-term financial benefit of spending a bit more on the product, but likely saving on installation costs and enjoying the peace of mind knowing they’ve installed a wall that should be expected to last for the next 100 years.
Redi-Rock gravity walls chosen to replace failing segmental retaining walls
Location: Liberty Lake, Washington
Redi-Rock installed in front of unstable SRW wall for new hotel development
Location: College Station, Texas
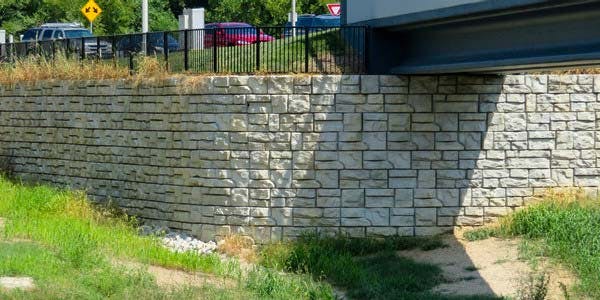
Wet cast the solution for freeze-thaw cycles instead of dry cast for bridge
Location: Chesterfield, Missouri